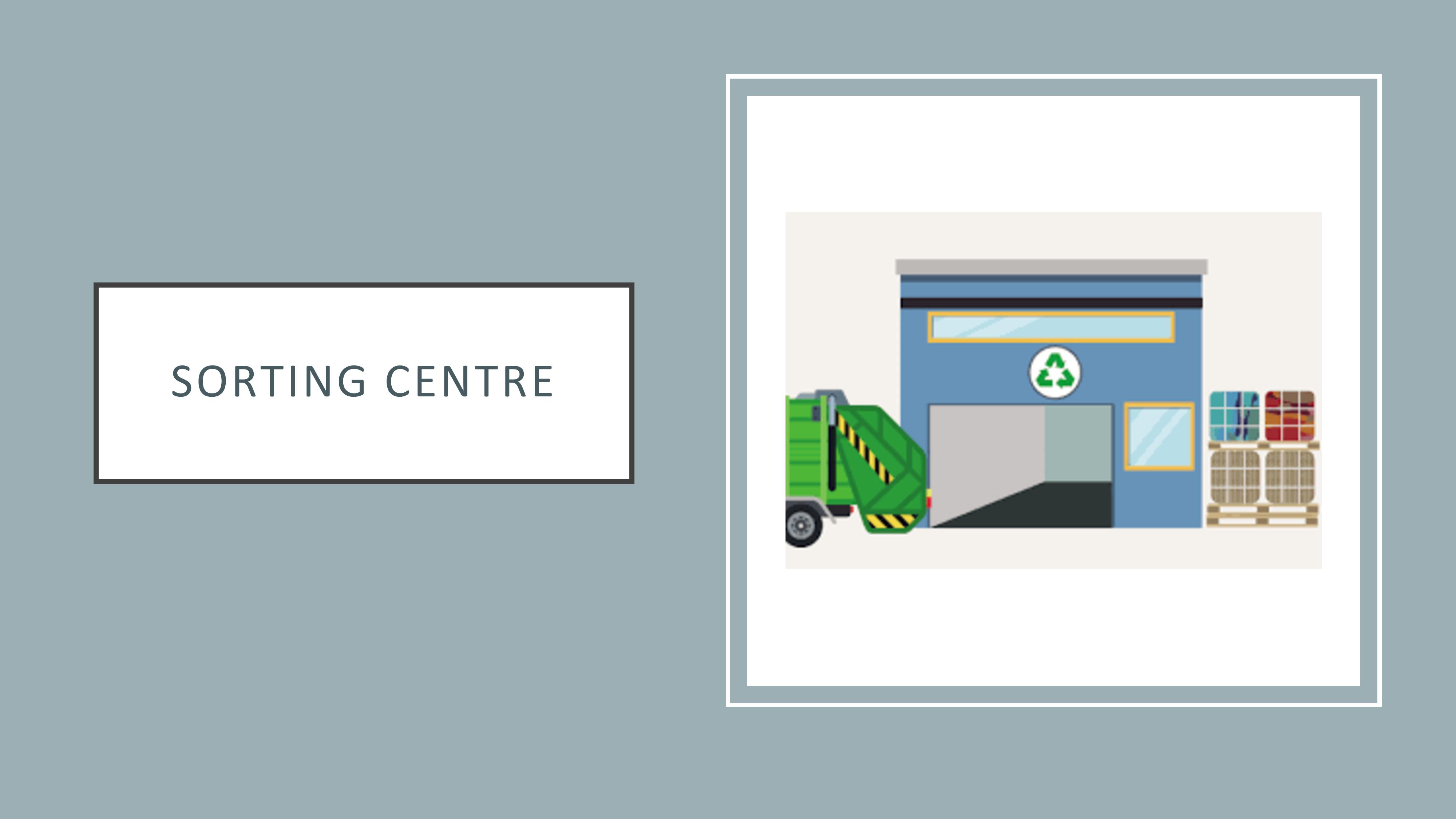
HOW WILL THE SORTING CENTER WORK ?
Sorting centre is basically a location where something is organised category wise and then processed. This is exactly what we aim to do in our model of the sorting centre for waste disposal. The model we are proposing for Paris is based upon and draws links from the Waste Sorting Centre in Marlborough, New Zealand.
So the Paris model would have arrondissement wise sorting centres i.e 20 sorting centres covering the region, one for every arrondissement. Pickups of waste will be scheduled twice a week initially but could be subject to change. Since this is a test stage, the number of pickups scheduled per week could be varied according to need and the population density of the area (number of people per unit area). This would mean that areas with higher population density could require more frequent pickups due to the more amount of people living there. Pickups will be scheduled Rue/Boulevard wise and a pickup schedule will be put into place. Each family/household would be assigned a barcode. This barcode will be unique to that particular family. The same barcode will also be present on the garbage disposal bags that the family will provide for the pickup.
TECHNOLOGY USED: BARCODE PRINTING
Barcode printing on disposal bags is something that is growing in popularity. It basically involves printing of barcodes on surfaces like plastic for help with identification. There are many real life examples as well as some companies that provide these services.
We can look to partner with one of these companies and sync their production schedules with our pickup schedules where in the second pick up for the week will provide the families with a new set of plastic bags and the plastic used to make these bags can be provided from the previous bags which will be recycled at the sorting centre. This way we ensure that the whole logistical chain is sustainable, renewable and reusable.
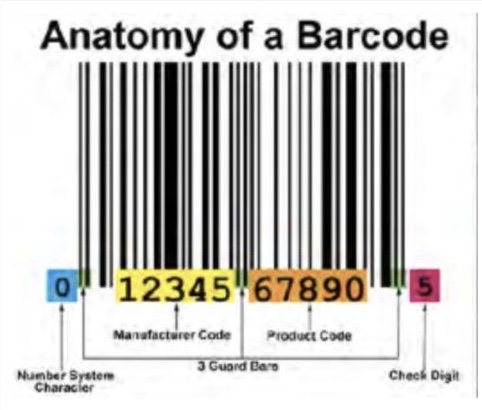
OPERATIONAL PROCEDURES OF THE CENTER
The sorting centre will categorise waste into 4 major divisions:
- Paper / Cardboard
- Plastic
- Glass / Metal
- Other
Thus each family will sort out their waste in these 4 categories and each of these categories will have a different colored plastic bag with the family’s barcode so that when the waste reaches the sorting centre they know how well the family has sorted the waste into the 4 categories.
Once the waste is received at the sorting centre, it will be inspected and perfectly categorised. The aim of this process will be to ensure that there is optimum allocation of waste via category and at the same determine the extent to which how well each family has categorised their waste before sending it to the centre.
The sorting centre will thus be divided into 4 parts with each part containing a conveyor belt where the waste will be disposed and then the inspection will be carried out. These conveyor belts will have the barcode triple scanner (as used by Lidl) linked to them to scan the waste bags and judge the quality of allocation.
The barcodes of the bag with improper allocation will be noted and an email/message sent to them regarding their improper allocation. Repeat offenders to be penalised. While on the other hand people with perfect allocation will be given incentives.
BAG’S IDENTIFICATION: THE TRIPLE SCAN
For the first step, which consists in identifying the origin of the garbage bag, we may use “triple scan” technology. This innovation has been developed by Lidl (it was at first dedicated to product’s barcodes detection in the large-scale distribution). But as its functioning is quite simple, we could easily adapt it to the garbage bags. Obviously, the only thing in common with a supermarket scanner would be the working principle. For the machine, we would use an industrial scan, whose cost is negligible on the factory scale (only few thousands of euros). It only requires two things: barcodes on several surfaces of the packaging, and three scanners (one horizontal downside, and two vertical on the sides). Thus, when the garbage bags are dropped one-by-one on the conveyor belt, one of the three scans will surely and automatically scan one of the multiple barcodes, which means it won’t need any human intervention in the process of identifying the origin of the garbage bag.
HUMAN INTERVENTION
Then, the larger part of the sorting is also automated. We just need few employees at this step, to check if some non-recyclable objects slipped into the wrong bags. If it is the case, they will push a button next to the conveyor chain. It will automatically send a message to the concerned household. The need for workforce will only depend on the quality of individual sorting, and thus on the public awareness campaigns. For the rest, the sorting will be insured by a complex combination of new technologies. It is very innovative compared to the current sorting centers which employs dozens of people for this arduous and exhausting work. ALTRIANE sorting center (Communauté d’Agglomération de La Rochelle) which employes 25 people. It may sounds a disproportionate work to do, but in fact, it is the case at the moment.
SORTING PROCESS
- Low separation: the ballistic separator
The three different flows (paper and cardboards ; plastics ; and aluminium or metal cans) would be separated by ballistic separators. A ballistic separator is a rotor that uses impellers to fling the different materials in the air. The materials are projected at different distance, depending on their weights. But having those three flows is not enough. Afterwards, three specific technologies will be used to sort metals, plastics and papers.
- Metal sorting; the magnetic separator
For the metal, we would use a magnetic separator. This system consists in a rotating magnetic drum, placed above the conveyor belt. It produces a magnetic field which attracts the ferrous particles. This step is crucial not only for obvious ecological reasons. It also prevents the employees from injuries (such as François Haslé’s “multiple scratches”). And it protects the material, as it takes off the ferrous particles larger than 3 mm.
- Plastic sorting: optical separator
The optical separator is without doubt the most complex technology on this chain[6], as it uses infrared spectrometry. Indeed, all the materials have a different specter, which can be used to identify them by comparing to a data base. Again, this scanner is placed above the conveyor chain. It analyses wastes’ specters within the space of few milliseconds, thanks to a processor. Once the material has been detected, the wastes are blown with compressed air canons towards different gutters. But one optical separator is not enough, as we can sort the materials depending on different criteria, such as fibrous material/flat material, hollow bodies/full bodies, polypropylene/polystyrene/others, etc. That is why we usually combine seven different optical separators, “in a cascade”, to refine the sort at each step.
- Waste packaging: the baling press
Conversely, this system is very simple but necessary at the end of the process. It compresses the materials to make bales, which eases the storage and handling.
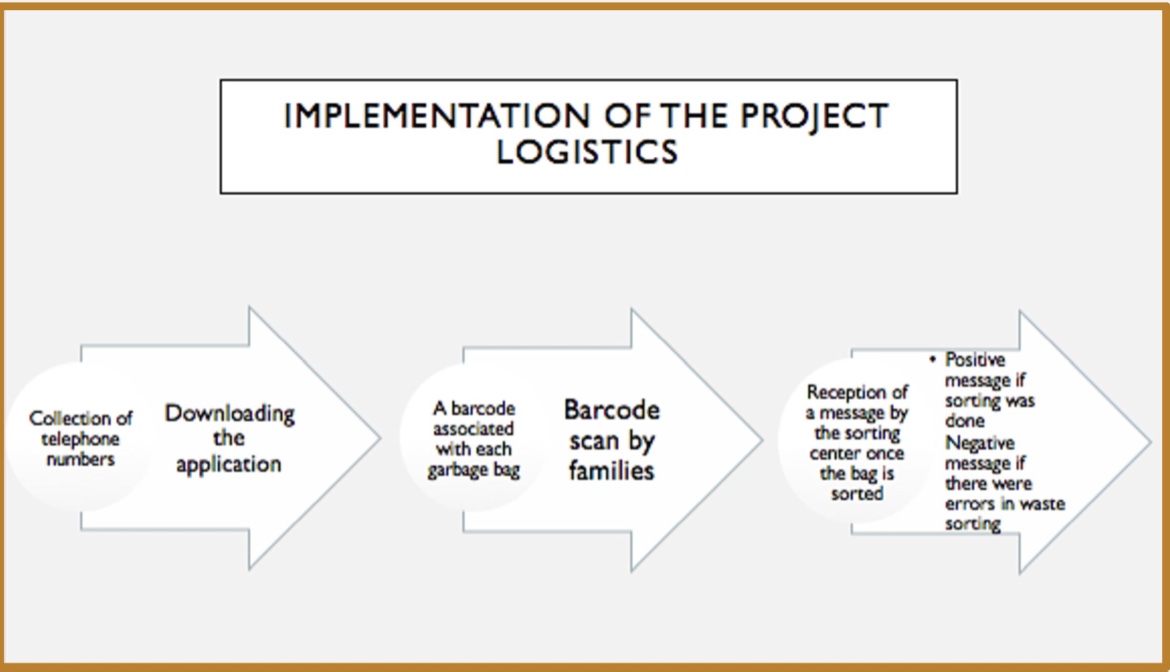